Sustainable Solutions and Cutting-Edge Tech: Key Drivers of Commercial Construction in 2025
In 2025, sustainable solutions and cutting-edge technologies are transforming commercial construction. You’re seeing significant reductions in waste and energy consumption through modular construction, which minimizes on-site waste by up to 83.2% and integrates sustainable materials like recycled steel and bamboo. Smart building technologies, including IoT sensors and building automation systems, optimize energy efficiency, security, and occupant comfort, cutting energy consumption by up to 29%[4]. Green building certifications like LEED and BREEAM guarantee adherence to environmental standards, while 3D printing and AI-driven tools streamline processes and enhance decision-making. As you move forward, these innovations will continue to drive efficiency, resilience, and sustainability in commercial construction.
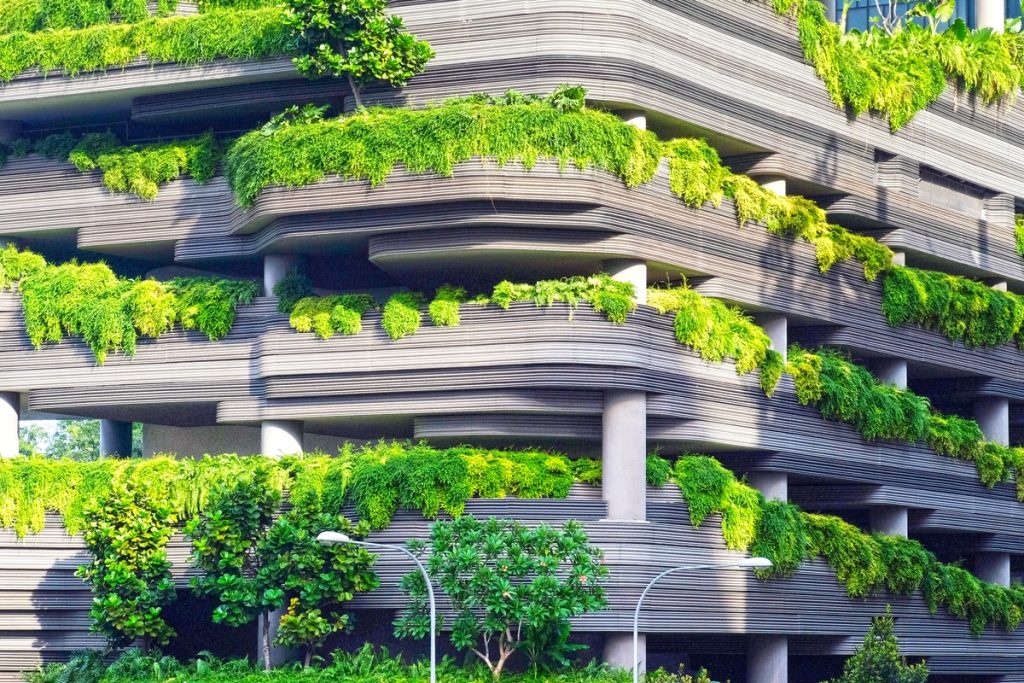
Introduction: The Future of Commercial Construction in 2025
In 2025, the commercial construction industry is poised to undergo a substantial transformation, driven by a strong emphasis on sustainability and technological innovation. As you navigate this evolving landscape, you’ll notice a profound shift towards sustainable construction practices. This includes the widespread adoption of green building certifications like LEED, WELL, and BREEAM, which validate buildings that meet stringent environmental and health standards.
Sustainability and Green Building Practices
As you explore the world of commercial construction projects in 2025, you’ll find that sustainability and green building practices are no longer optional, but essential. The industry is witnessing a significant upsurge in environmentally friendly construction methods, driven by regulatory demands, cost savings, and brand identity.
Green building certifications like LEED and BREEAM are becoming benchmarks for sustainability. These certifications promote the use of energy-efficient materials, waste reduction, and improved indoor air quality. For instance, net-zero energy designs, which incorporate technologies like solar panels, wind turbines, and advanced energy storage, are gaining traction. Modular construction methods, involving off-site prefabrication, are also on the rise, minimizing waste and reducing transportation emissions.
Modular construction, coupled with the use of low-carbon and recycled materials such as bamboo, recycled steel, and sustainable concrete, enhances durability and energy efficiency. Green roofs and vertical gardens further contribute to air quality improvement, insulation, and stormwater management. These sustainable practices not only reduce the environmental impact but also attract tenants and buyers who prioritize sustainability, making them a strategic investment for the future.
Smart Technology and Building Automation
Building on the robust adoption of sustainable construction practices, the integration of smart technology and building automation is set to revolutionize the commercial construction industry in 2025. You will see a significant shift towards smart building technologies that enhance energy efficiency, security, and occupant comfort. These intelligent structures, equipped with IoT sensors and automation, can adjust systems like lighting, heating, and cooling based on real-time data, reducing energy consumption and operational costs.
In the DFW area, for instance, commercial construction companies are increasingly incorporating building automation systems (BAS) that optimize HVAC, lighting, and security. These systems, when properly integrated and maintained, can cut energy consumption by up to 29%, as evidenced by studies on commercial building controls[2][5].
AI-driven tools will also play a vital role, forecasting project timelines, optimizing resource allocation, and predicting potential delays and risks. Additionally, technologies like 3D printing and prefabrication will streamline construction processes, reducing labor costs and material waste while enhancing safety and customization options[1][4].
Modular and Prefabricated Construction
How can modular and prefabricated construction transform the efficiency and sustainability of commercial building projects in 2025.By adopting modular and prefabricated construction methods, you can substantially improve the sustainability and efficiency of your commercial building projects. These approaches involve constructing building elements in controlled factory environments, which reduces on-site waste by up to 83.2% and minimizes the impact of weather conditions.
Modular construction allows for the integration of sustainable materials and technologies more effectively. You can use recycled materials, energy-efficient designs, and renewable energy sources, aligning your projects with green building standards like LEED and BREEAM. This not only reduces the carbon footprint during production but also during the building’s operational life.
The efficiency gains are substantial as well. Modular construction can reduce construction time by up to 50%, enable parallel on-site and off-site work, and lower labor costs due to efficient production methods. The controlled factory environment guarantees consistent quality, standardized processes, and the integration of advanced technologies, making the entire process more reliable and cost-effective.
Energy Efficiency and Net-Zero Buildings
In the pursuit of a more sustainable future, energy efficiency and the achievement of net-zero buildings are at the forefront of commercial construction in 2025. As you navigate the evolving landscape of new construction, incorporating net-zero energy designs is no longer a luxury, but a necessity. The upcoming updates to the National Construction Code (NCC) in 2025 will mandate stringent energy-efficiency requirements, pushing facility managers and builders to adopt innovative solutions.
High-performance building materials, such as advanced glazing and insulated precast concrete panels, are vital for minimizing heat loss and reducing the need for artificial climate control. These materials not only enhance energy efficiency but also cut down on heating and cooling costs. Smarter backup power systems, including specialized battery systems, guarantee continuous operation of critical infrastructure during power outages, reducing downtime and environmental impact.
Net-zero energy buildings, which match renewable energy production with consumption, are a key focus. Examples like the National Renewable Energy Laboratory’s Research and Support Facility demonstrate how advanced heat recovery technologies, photovoltaic power, and energy-efficient design can achieve net-zero site energy goals. By integrating these strategies, you can create commercial buildings that are not only energy-efficient but also resilient, health-conscious, and environmentally responsible[1][5][3].
Circular Economy and Waste Reduction
As the construction industry embraces sustainable practices, the circular economy and waste reduction have become integral components of commercial building projects in 2025. You’re likely to see a significant shift from the traditional linear “take-make-dispose” model to a more regenerative and resource-efficient approach. This change is driven by the need to reduce the substantial environmental footprint of the construction sector, which accounts for approximately 40% of global waste production.
In commercial construction projects, adopting circular economy principles can lead to substantial cost savings and environmental benefits. For instance, implementing material recovery strategies can lower construction costs by 15-25% through mechanisms like systematic demolition and careful material sorting. Merit contractors, Inc., and other industry leaders are embracing these practices, salvaging valuable resources like steel, copper, and timber for reuse or resale, thereby reducing waste disposal fees and raw material purchases[1][3].
The use of modular construction systems, material passport platforms, and waste-to-resource technologies is also on the rise. These innovations enable better tracking and management of materials, ensuring they remain valuable resources rather than waste. By designing buildings for disassembly and reuse, the industry can enhance building resilience and reduce the frequency of major repairs or rebuilds, aligning with the broader goals of sustainability and resource efficiency[1][3][5].
Advanced Construction Materials
Advanced construction materials are at the forefront of the industry’s shift towards sustainability and efficiency. In 2025, you will see a substantial emphasis on materials that not only reduce environmental impact but also enhance the performance and durability of buildings.
One of the key materials gaining traction is low-carbon concrete. This innovative material, such as geopolymer concrete, uses industrial by-products like fly ash or slag instead of traditional Portland cement, reducing the carbon footprint by up to 80% while maintaining or exceeding the strength and durability of conventional concrete[4].
Insulated Concrete Forms (ICFs) are another advanced material that combines the structural strength of concrete with the energy efficiency of foam insulation. These forms create highly insulated walls that provide exceptional thermal performance, reducing the need for additional heating and cooling[2].
Smart glass is also transforming building envelopes by allowing windows to change opacity in response to environmental conditions, markedly improving energy efficiency and occupant comfort. Additionally, materials like hempcrete, rammed earth, and recycled steel are being increasingly adopted for their energy-efficient and sustainable properties[4][5].
These advanced materials, when integrated with smart building technologies and modular construction methods, will help you create buildings that are not only sustainable but also resilient and energy-efficient.
AI and Robotics in Construction
The integration of advanced construction materials sets the stage for the next significant leap in sustainability and efficiency: the adoption of AI and robotics in construction. As you navigate the evolving landscape of commercial construction in 2025, you’ll find that AI, robotics, and autonomous systems are revolutionizing how projects are planned, executed, and managed.
AI is at the forefront, enabling data-driven decision-making, predictive analytics, and automated process optimization. It helps predict project delays, identify potential problems, and optimize resource allocation, ensuring smoother and more efficient project management[3][4].
Robotics is transforming various aspects of construction, from automated bricklaying systems that can lay up to 3,000 bricks per day, to 3D printing and additive manufacturing that can construct entire buildings within days. Demolition and renovation robots enhance safety by handling hazardous tasks, while AI-powered drones streamline site surveys and safety inspections[1][5].
Autonomous machines, equipped with GPS, LiDAR, and IoT sensors, are becoming standard, increasing productivity and safety by operating 24/7 without fatigue. AI and machine learning are making these robots smarter, enabling them to adapt to site conditions and optimize workflows[5].
3D Printing in Construction
In the domain of commercial construction in 2025, 3D printing is emerging as a game-changer, revolutionizing how structures are designed, built, and managed. This technology substantially reduces material waste by using only the necessary amounts of materials, a stark contrast to traditional construction methods which often generate excess waste. According to industry research, 3D printing can reduce material consumption by 30-60% compared to other methods, making it a vital tool for sustainable construction[3/.
You will see 3D printing integrating eco-friendly materials, such as locally sourced micro-concrete formulations, which require less water and emit fewer carbon emissions during production. This approach not only enhances the longevity and durability of construction projects but also minimizes waste and optimizes resource utilization[1].
The scale and volume of 3D printed construction projects are set to increase, with advancements in material science and multi-material printing. Real concrete, offering greater strength, flexibility, and sustainability, will become more prevalent, replacing dry-mix mortars. Automated construction using multi-functional 3D printers will also streamline the process, reducing overall construction time and costs[5].
As you adopt 3D printing, you’ll benefit from localized manufacturing, reducing transportation emissions and supporting regional economies. This technology aligns perfectly with the industry’s growing commitment to sustainability, enabling the creation of net-zero energy buildings, green roofs, and resilient infrastructure[4].
Urban Sustainability and Resilient Infrastructure
As you integrate 3D printing into your construction projects, you’re also contributing to a broader shift towards urban sustainability and resilient infrastructure. In 2025, urban sustainability will be a cornerstone of commercial construction, driven by the need for environmentally responsible and durable buildings. Cities are focusing on developing smart infrastructure that supports sustainability and connectivity, including the construction of green buildings, efficient public transportation systems, and smart grids.
Resilient infrastructure is another critical aspect, with buildings designed to withstand natural disasters and climate change impacts. This involves using low-carbon and recycled materials, such as recycled steel, bamboo, and sustainable concrete, which not only reduce the carbon footprint but also enhance the structural integrity of the buildings[1][3][4].
Smart building technologies will play a crucial role in urban sustainability, with automated systems managing energy usage, lighting, and security. These systems optimize energy consumption based on occupancy and usage patterns, leading to significant cost savings and reduced environmental impact. Additionally, modular construction methods will expedite project completion times while minimizing waste and transportation emissions, further aligning with urban sustainability goals[1][3][4].
Building Health and Wellness
Building health and wellness are becoming paramount in commercial construction, as architects and builders increasingly focus on creating environments that promote occupant well-being. This shift is driven by the understanding that the built environment markedly impacts the physical and mental health of its occupants. In 2025, you can expect to see a rise in the incorporation of smart building technologies that enhance indoor air quality, lighting, and temperature, all of which are vital for maintaining a healthy indoor environment.
Green roofs and vertical gardens, for instance, not only enhance urban aesthetics but also improve air quality and provide insulation, reducing the need for extensive HVAC systems[3][4]. The use of low-carbon and recycled materials, such as bamboo, recycled steel, and reclaimed wood, also contributes to healthier indoor environments by reducing the presence of volatile organic compounds (VOCs) and other pollutants.
Additionally, AI and machine learning are being integrated to monitor and adjust building conditions in real-time, ensuring that the environment remains ideal for occupant health. These technologies can analyze occupancy patterns and adjust lighting, heating, and cooling accordingly, enhancing both comfort and energy efficiency[1][5]. By prioritizing building health and wellness, commercial construction projects can create spaces that are not only sustainable but also conducive to the well-being of their occupants.
Conclusion
The commercial construction industry in 2025 is poised for a transformative shift, driven by the integration of sustainable practices and cutting-edge technologies. As you navigate this new landscape, it’s clear that sustainability is no longer a secondary consideration, but a core principle. Green building certifications like LEED, WELL, and BREEAM are becoming indispensable, encouraging the use of energy-efficient materials, waste reduction, and improved indoor air quality[3][4%.
Technological innovations such as AI, robotics, and 3D printing are revolutionizing project execution. AI and machine learning are enhancing decision-making, reducing risks, and boosting productivity by analyzing vast amounts of data. Robotics and 3D printing are streamlining processes, reducing waste, and enabling faster construction times. Modular construction, in particular, allows for efficient assembly and extensive customization, making it a preferred method for many developers[1][5].
As you adopt these trends, you’ll be contributing to a more resilient, health-conscious, and environmentally responsible built environment. The focus on net-zero energy designs, circular economy principles, and energy-efficient materials will drive long-term sustainability and reduce environmental impact. By embracing these innovations, you’ll not only stay competitive but also build a greener, smarter, and more sustainable future for commercial construction. This strategic integration of technology and sustainability will be the hallmark of successful projects in 2025 and beyond.