Prefabricated vs. Traditional Construction: A Game-Changer for DFW Commercial Spaces
In the bustling commercial landscape of DFW, prefabricated construction is a game-changer, offering significant advantages over traditional methods. You can expect reduced construction time by up to 50% due to parallel processing, where components are fabricated simultaneously in controlled factory environments. This approach also leads to cost savings through efficient material use and lower labor requirements. Additionally, prefabrication enhances sustainability by minimizing waste and energy consumption, and it guarantees higher quality control with fewer defects. With faster project completion, reduced disruptions, and long-term durability, prefabricated construction is revolutionizing the way buildings are erected in DFW, making it an attractive option for those looking to streamline their projects efficiently. By embracing this method, you can achieve faster operational readiness, cost savings, and a more sustainable building process, so it’s worth exploring further to see how it can benefit your next commercial project.
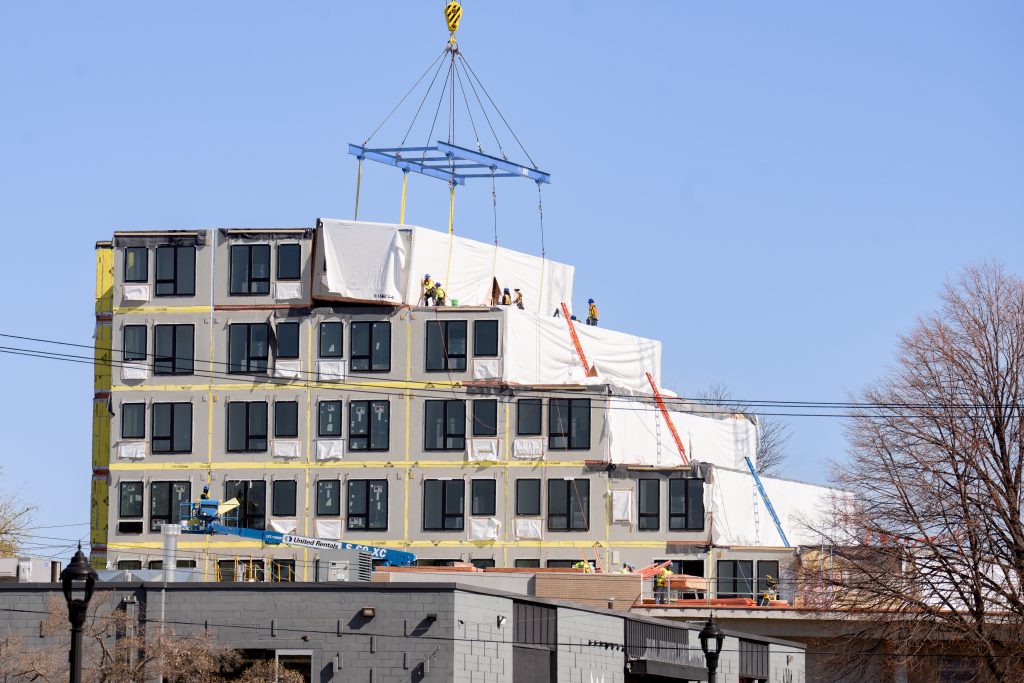
Introduction: Prefabricated vs. Traditional Construction in DFW Commercial Spaces
In the rapidly evolving DFW commercial real estate market, the choice between prefabricated and traditional construction methods is becoming increasingly important for developers and business owners. As you consider your next commercial project, understanding the differences between these two approaches can help you make an informed decision.
Prefabricated construction involves the off-site fabrication of building components, which are then assembled at the construction site. This method offers several key advantages, including reduced construction time and cost savings. By manufacturing components in a controlled factory environment, prefabrication allows for parallel processing, substantially reducing the overall project duration. This can be particularly beneficial in meeting tight deadlines and minimizing disruptions to surrounding areas[2][3][5].
In contrast, traditional commercial construction services is more labor-intensive and often results in longer timelines and higher costs. This method is better suited for complex or custom-designed projects where the flexibility in design is vital. However, for many commercial projects in DFW, the efficiency, speed, and quality control of prefabricated construction make it an attractive option. By choosing prefabricated construction, you can leverage economies of scale, reduce material waste, and maintain high-quality standards, making it an ideal choice for urban development in the DFW area[1][3][5].
Prefabricated Construction Overview
Prefabricated construction offers a robust and efficient alternative to traditional building methods, particularly in the fast-paced DFW commercial real estate market. This approach involves the off-site fabrication of building components, which are then transported and assembled at the construction site. One of the primary advantages of prefabricated construction is the significant reduction in construction timelines. By allowing for parallel processing, where different components are constructed simultaneously, you can meet tight deadlines and minimize disruptions to surrounding areas[1][4][5].
Prefabrication also leads to substantial cost savings. The efficient use of materials in a factory setting reduces waste and minimizes labor requirements, contributing to lower overall project costs. Additionally, the controlled environment guarantees better quality control, resulting in higher-quality buildings with fewer defects and less need for costly rework[1][2][4].
Moreover, prefabricated construction enhances sustainability by optimizing material usage and reducing waste. This method produces less waste and uses less energy during construction, making it a more environmentally friendly option. With prefabrication, you can achieve faster, more efficient, and sustainable building solutions, making it an ideal choice for urban development in the DFW area[3][5].
Traditional Construction Overview
Traditional construction, while still a viable option for many projects, involves a more labor-intensive and time-consuming process compared to prefabricated methods. This approach requires all construction stages to take place on-site, where skilled craftsmen perform manual, hands-on work. This method can result in buildings with unique character and craftsmanship, as each project is often customized and distinct from others.
One of the key advantages of traditional construction is the flexibility it offers in material selection and design adjustments. Locally sourced materials can be used, which can sometimes lower material costs and guarantee the building blends seamlessly with its surroundings. Additionally, traditional construction allows for effective teamwork and continuity in workflow, as the same people are involved from start to finish, enhancing efficiency and effectiveness.
However, traditional construction methods have significant drawbacks. They are generally more costly and time-consuming due to the reliance on specialized labor and sequential construction phases. Changes in design during the project can be challenging to implement, potentially delaying the timeline further. Furthermore, the lack of controlled environments for material storage and work can lead to material waste and quality issues, making it less sustainable compared to modern methods like prefabrication[1][3][5].
Impact of Prefabricated Construction on DFW Commercial Spaces
The rapid adoption of prefabricated construction in the DFW real estate market is transforming the way commercial spaces are built, offering a slew of benefits that cater to the region’s demanding development landscape. For developers in DFW, prefabricated construction is a game-changer, particularly for modular office buildings. This method substantially reduces construction time, allowing you to meet tight deadlines and get your commercial spaces operational sooner. By manufacturing building components off-site, you minimize on-site labor requirements and reduce the need for extensive site management, which in turn lowers labor and material costs[2][4].
Prefabricated construction also has a profound impact on sustainability. It produces less waste, as components are made in a controlled factory setting where recyclable materials can be easily separated and reused. This approach can reduce construction waste by up to 83.2%, a considerable advantage over traditional methods[3][5].
Additionally, prefabricated buildings are more energy-efficient and durable. They incorporate energy-saving features such as solar panels and improved wall insulation, reducing long-term utility costs. The controlled factory environment guarantees higher quality control, tighter joints, and better air filtering, contributing to a healthier indoor environment and reduced environmental disturbance[1][3]. These benefits make prefabricated construction an ideal choice for the fast-paced DFW real estate market.
Conclusion: The Future of Commercial Construction in DFW
As you consider the future of commercial construction in the DFW area, you might wonder: What role will prefabricated construction play in shaping the region’s building landscape? Given the compelling advantages of prefabricated construction, it is clear that this method will become increasingly integral to the region’s development.
Prefabricated construction offers significant time and cost savings, allowing projects to be completed 30-50% faster than traditional methods[1][3][5]. This efficiency is particularly valuable in the DFW market, where rapid development and meeting tight deadlines are vital. Additionally, the controlled factory environment guarantees higher quality control and reduces waste, aligning well with the growing emphasis on sustainability in urban development.
As the demand for commercial spaces continues to rise, incorporating prefabricated construction into design-build services can streamline the entire project process. By leveraging prefabrication, developers can maintain high-quality standards while reducing on-site labor requirements and managing site coordination more effectively[2][4]. This approach not only accelerates project timelines but also enhances the overall efficiency and cost-effectiveness of commercial construction in the DFW area. As the region continues to grow, prefabricated construction is poised to play a pivotal role in its future building landscape.